The Future of Modular and Prefabricated Construction: Is This the Answer to Australia's Housing Crisis?
- Steve G
- Jan 11
- 4 min read
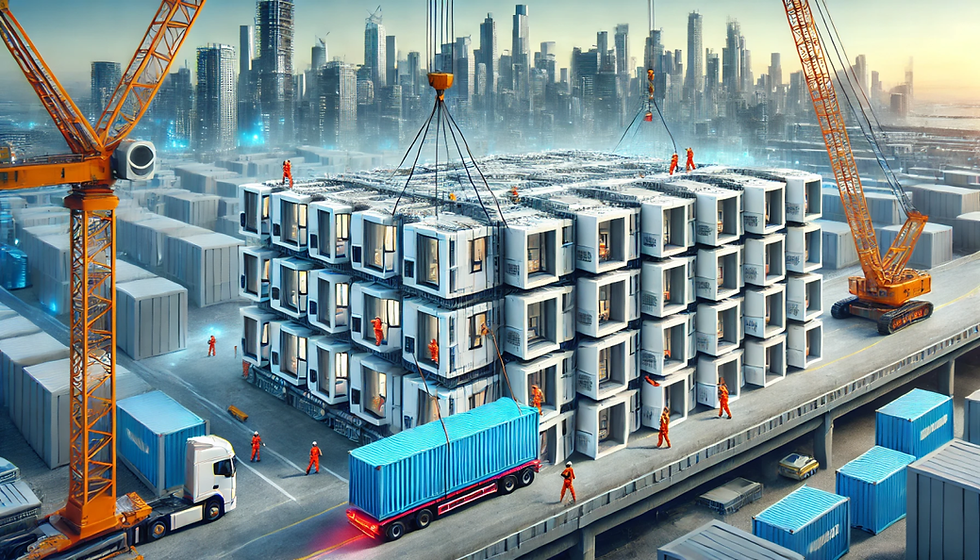
Australia is facing a growing housing crisis. With demand for affordable housing far outstripping supply, the construction industry is under pressure to find innovative solutions. One approach gaining traction is modular and prefabricated construction, methods that promise faster, cheaper, and more sustainable ways to build. But can these technologies really provide a solution to Australia’s housing shortage?
In this article, I’ll explore the benefits, challenges, and future potential of modular and prefabricated construction in Australia, and whether this method is a realistic answer to our housing woes.
What is Modular and Prefabricated Construction?
Modular construction involves creating building components—often entire rooms or sections—offsite in a controlled environment. These modules are then transported to the construction site, where they are assembled to create a complete structure. Prefabricated construction refers to the broader practice of manufacturing building components offsite, including wall panels, roofs, and floors, which are later assembled onsite.
The appeal lies in the efficiency of the process. By moving part of the construction offsite, modular and prefabricated methods can cut project timelines in half, reduce costs, and limit material waste . In a market desperate for more affordable homes, these are compelling benefits.
How Could This Address Australia's Housing Crisis?
Speed and Efficiency
Australia’s housing shortage is a pressing issue, and traditional construction methods are struggling to keep up with demand. Modular construction offers a faster alternative. Since much of the work is done offsite, weather delays and site-related disruptions are minimized. Projects can be completed in a fraction of the time compared to traditional methods .
For example, some modular construction projects can be completed in 50% less time than conventional builds . This speed could be crucial in meeting the high demand for housing in urban areas like Sydney and Melbourne.
Cost Reduction
Modular and prefabricated methods are also cost-effective. Manufacturing parts offsite in a factory setting allows for better control over materials, reducing waste and ensuring that projects stay within budget. The use of standardized processes can also lead to significant savings . For affordable housing projects, this cost reduction is vital.
In Australia, rising labor costs have been a key driver of housing price increases. Prefabricated construction requires fewer workers onsite, further reducing costs .
Sustainability
Modular and prefabricated construction also aligns with the growing focus on sustainability in the construction industry. These methods reduce the environmental impact by minimizing waste and energy consumption during the construction process . Buildings can also be designed to be energy-efficient, aligning with Australia’s push for greener, more sustainable urban development .
The Challenges of Modular and Prefabricated Construction
Despite its potential, modular and prefabricated construction faces significant challenges in Australia.
Perception and Acceptance
There remains a perception that prefabricated buildings are of lower quality than traditional homes. This stigma can deter buyers and developers, despite the fact that modern modular buildings often meet or exceed traditional standards . Overcoming this perception will be key to broader adoption.
Regulatory Barriers
Australia’s building regulations can be a barrier to modular construction. Prefabricated methods don’t always fit neatly into the country’s existing regulatory framework, which was developed with traditional construction in mind. Navigating these complexities can add time and cost to projects .
Logistical Challenges
While modular construction works well in densely populated urban areas, it can be more difficult in remote or regional locations. Transporting large modules across long distances can be costly and complex .
What Does the Future Hold?
Despite the challenges, the potential for modular and prefabricated construction in Australia is undeniable. As housing demand continues to rise, developers, policymakers, and builders will need to innovate to meet the needs of the population. The Australian government has already begun exploring ways to support this shift, with initiatives aimed at encouraging more sustainable and efficient building practices .
The future of construction may not entirely replace traditional methods, but modular and prefabricated options could play a crucial role in delivering affordable, sustainable housing more quickly and efficiently.
Conclusion
Modular and prefabricated construction offers significant potential to address Australia’s housing crisis by improving speed, cutting costs, and reducing environmental impact. However, overcoming regulatory challenges, changing public perception, and navigating logistical complexities will be key to its widespread adoption.
Is this the solution we’ve been waiting for? Only time will tell, but one thing is clear: we must continue to innovate to build the homes Australians need.
About Dr. Stephen Gardner
Dr. Stephen Gardner, Gold Coast is an experienced property developer and construction industry thought leader. With a PhD focusing on the technical and interpersonal skills of successful construction project managers, Stephen has a passion for driving change in the industry. His research and hands-on experience offer unique insights into sustainability, workforce development, and industry trends in Australia. Stephen regularly writes on topics ranging from leadership and innovation to workforce training and environmental responsibility.
References
Modular Building Institute, “Modular Construction Report 2023”
PrefabAUS, “The Prefabrication Advantage: Efficiency in Building”
Construction Industry Council, “Modular Construction and Housing Demand”
Australian Construction Journal, “Speeding Up Housing Supply with Modular Construction”
McKinsey & Company, “Modular Construction: From Projects to Products”
Australian Bureau of Statistics, “Impact of Rising Labor Costs on Housing Prices”
Green Building Council Australia, “Sustainability in Modular Construction”
Australian Government Department of Industry, Science, Energy, and Resources, “Energy Efficiency in Construction”
Australian Institute of Architects, “Changing Perceptions of Prefabricated Homes”
Property Council of Australia, “Regulatory Challenges in Prefabricated Construction”
Transport Infrastructure Council, “Logistics of Modular Construction in Regional Australia”
Australian Government Housing Initiative, “Encouraging Innovation in Construction”
Comments